Welding mistakes can shorten your equipment’s lifespan. Discover 5 critical welding errors that hurt durability and how to prevent them. Read now.
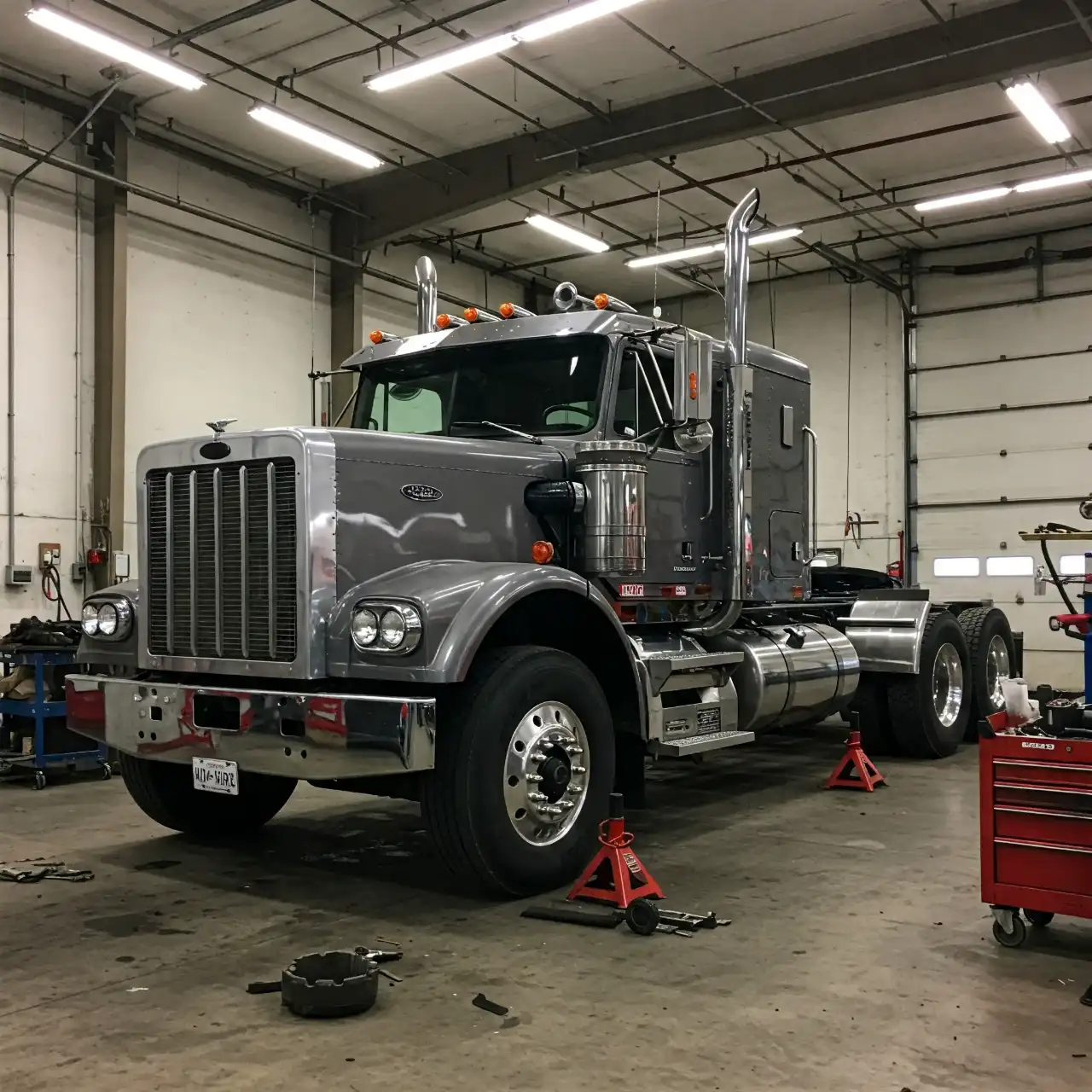
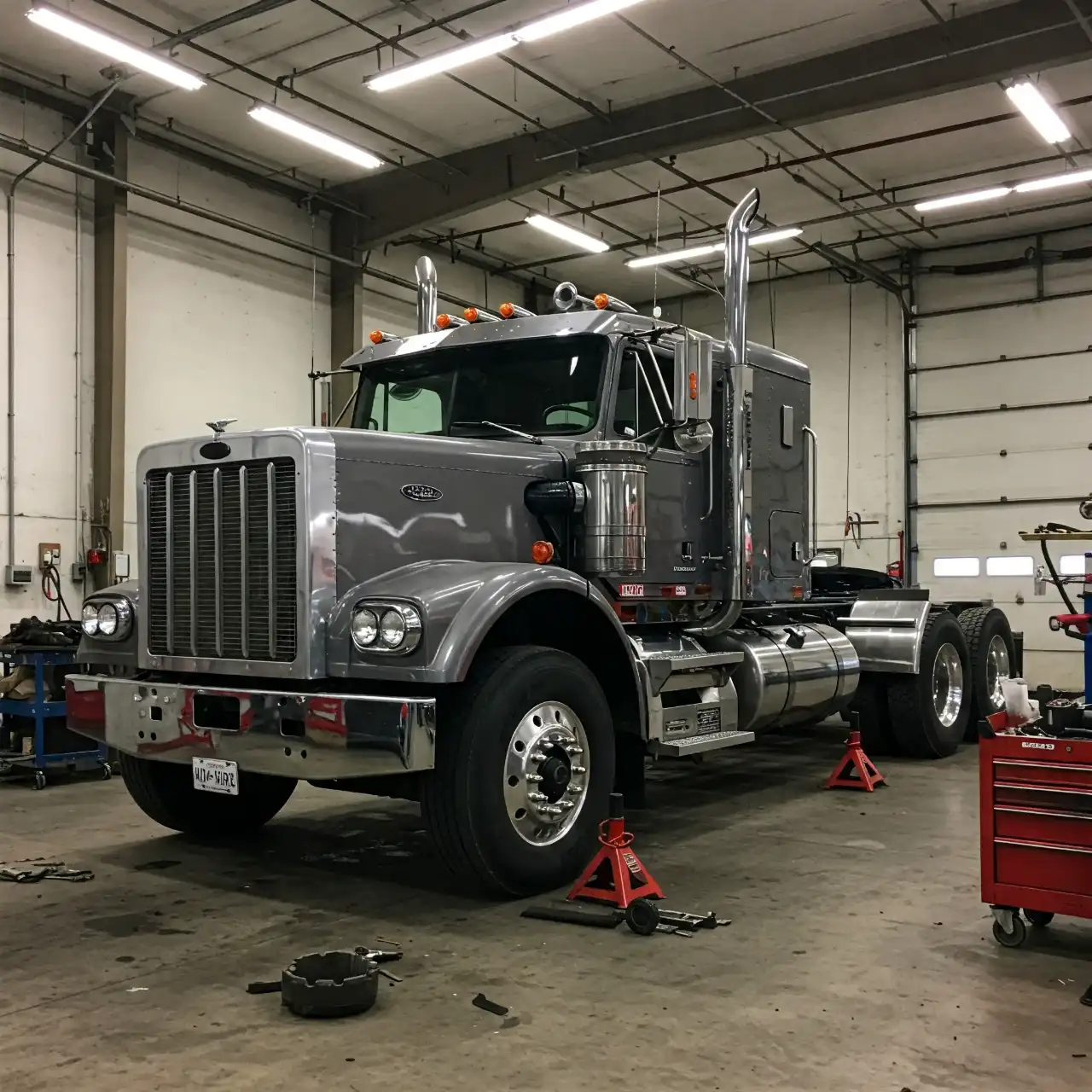
Welding is one of those tasks that looks simple from the outside—sparks fly, metal melts, and hey presto, things stick together. But if you're a professional welder in the heavy-duty repair business, you know it's not that straightforward. A single mistake during welding can undermine the durability of your equipment, leading to breakdowns, unsafe operation, and steep repair bills.
Whether you're patching up a cracked chassis or fabricating a custom bracket, avoiding these common welding mistakes is critical to keeping your fleet road-ready and reliable.
1. Skipping Proper Surface Preparation
Let’s not sugarcoat it: dirty metal makes for dirty welds. Contaminants like rust, oil, grease, and even paint act as barriers, preventing proper fusion. When a weld can't fully penetrate or bind, it becomes brittle and prone to cracking—especially under the stress heavy-duty equipment endures.
Best practice: Grind, sand, or use a wire brush to clean the surface. If you’re dealing with stainless or aluminum, use a dedicated prep tool to avoid cross-contamination from carbon steel.
2. Incorrect Heat Settings
Welding is all about heat control. Too much, and you burn through the material. Too little, and your weld sits there freezing, well, maybe not freezing, but not hot enough to get the job done. The result? Weak, porous welds that can split or shear under torque or vibration.
Heavy-duty components—like frame rails or axle mounts—require precision. Always match your amperage to the material thickness and take into account the welding position and joint type. When in doubt, test weld on a scrap piece first.
3. Neglecting Joint Design and Fit-Up
Ever tried welding a sloppy gap or misaligned joint? It's a nightmare. Poor joint preparation forces you to bridge gaps with filler metal, which weakens the weld and can distort structural alignment. That’s a big no-go for parts like suspension brackets or trailer hitches.
Tip: Use clamps and jigs to secure workpieces and ensure tight fit-up. When repairing high-stress areas—such as crossmembers or control arms—always recreate the original joint geometry to preserve structural integrity.
4. Lack of Penetration and Fusion
A weld that just "sits there" without penetrating is nothing more than a decorative bead. Without proper fusion into the base metal, the weld won’t hold under load. This mistake often occurs with fast travel speed, low heat, or incorrect technique.
You can’t cut corners here. Full penetration welds are essential for critical repairs, especially on load-bearing parts like fifth-wheel plates or frame extensions. Consider using a multi-pass technique if you're welding thick material.
5. Skipping Post-Weld Inspection and Testing
Welds may look good on the surface but hide flaws beneath. Internal cracks, porosity, or inclusions can lurk inside, waiting to fail under pressure.
Don't leave your shop open to liability. Always inspect your welds visually for uniformity and consistency. For high-stakes repairs, perform non-destructive testing (NDT) like dye penetrant, magnetic particle, or ultrasonic testing, especially if the vehicle will be hauling across Chicago Heights' rough winter roads.
Welding the Right Way Keeps Your Fleet on the Road
Remember, one bad weld could lead to downtime, DOT violations, or roadside failures. By prioritizing proper technique, preparation, and inspection, you're building more than strong welds—you're building trust and long-term durability into your fleet.
Are you not sure if your weld repairs are holding up? Take a proactive approach—inspect previous repairs, revisit your shop’s welding protocols, and ensure your techs are trained on best practices. When equipment uptime is everything, every weld counts.
News & Articles
Read About The Latest in Industry
Here, you'll find regular articles covering a wide range of topics related to diesel repair, maintenance, and troubleshooting. Whether you're an operator, fleet manager, or diesel engine enthusiast, you'll find something of interest here.
Don't Take our word for it.
Read Customer Testimonials.
"I've been taking all my company Trucks and equipment to Fleet Tech for the last 10 years. These guys really are the best around, they are some of the most understanding people I've ever met! They get it fixed and they do it right! You won't have to worry a bit if you take something here."
"Everyone over at Fleet Tech is amazing. From the office staff to the guys out in the field. A++ operation all the way around. Highly recommended for all your fleets needs! Testimonial written by Matt S. on this site."
"Best of the best! They always get me back on the road when my stuff breaks down."
Contact Us
Get in touch with Fleet Tech Inc. today to schedule professional diesel mechanic services in the Chicago Heights, Illinois area!